Prototyping
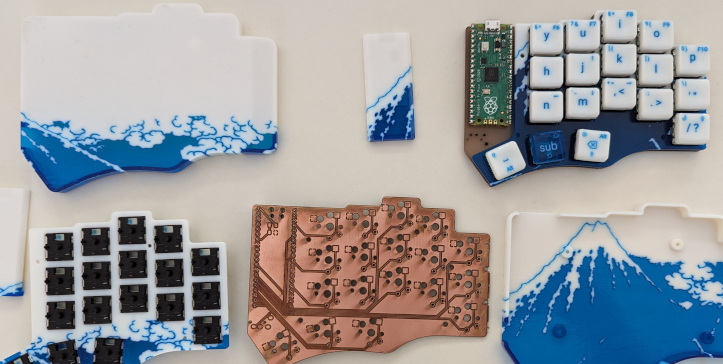
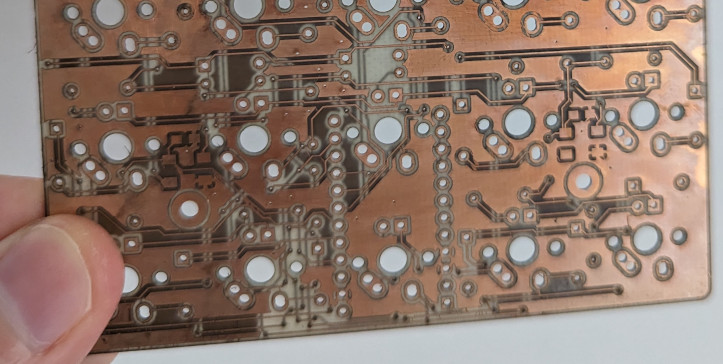
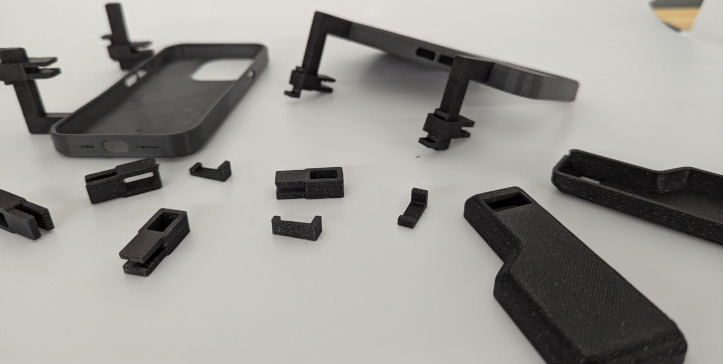
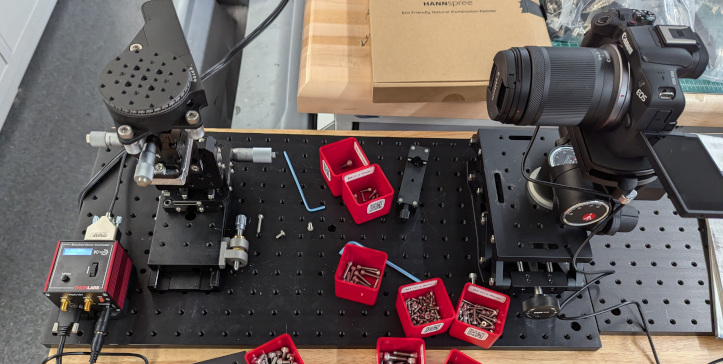
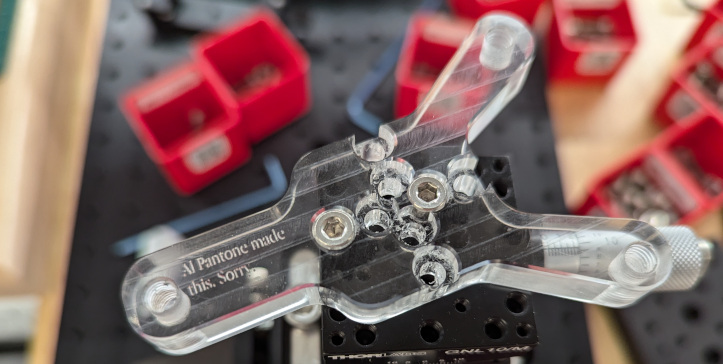
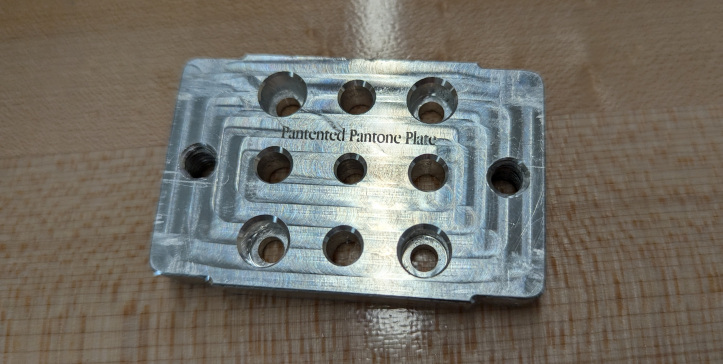
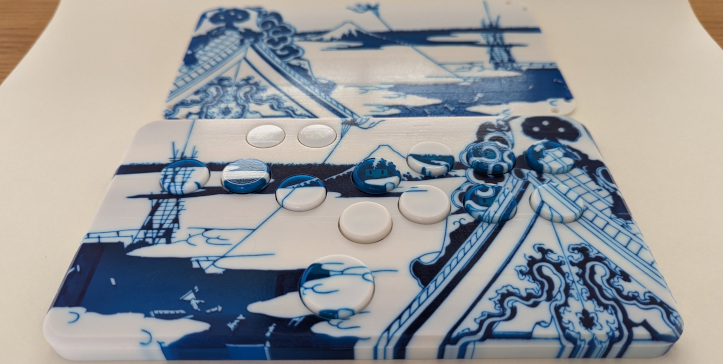
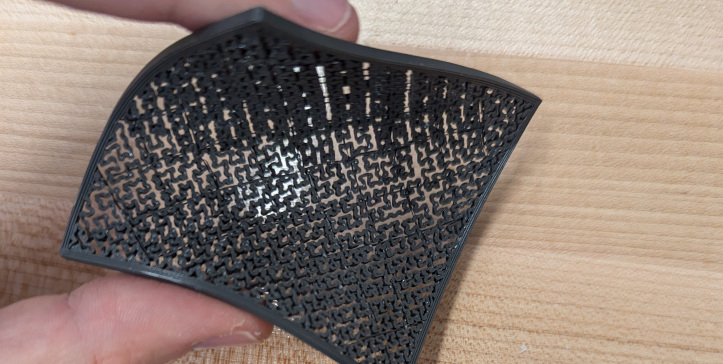
Prototyping
My primary job at Apple is prototyping; always trying to push the boundrary of what it's possible for us to build. It's wonderful work, and I find it just as rewarding to build a cool new thing as it is to build a tool that allows someone else to build a cool new thing.
Virtually all of my work is confidential, but I am able to share these designs, which were made either as part of material/process validation or were made to interface with external tools. The keyboard and controller cases are heavily modified existing designs printed on a resin-jet 3d printer. I created the graphic design portion of these from scratch based on Hokusai's Thirty-six Views of Mount Fuji, it is purely cosmetic. I designed all the keycaps from scratch. I made the PCB the lab's laser cutter as part of a larger project to wrangle all our presets and material libraries into one universal bundle.
As part of a larger effort I led to expand our global lab capabilities, I shepherded a policy change at Apple to allow the use of new 3d printing software and processes. Part of that was making samples to demonstrate where our labs lacked necessary capabilities, such as designing and building a fixture to accurately hold measuring equipment on an iPhone from a rigid material embedded inside a flexible case (an ask from the Display Incubation team), and partnering with the soft goods team to create a 3d-printed knit mesh material that is not possible to make from any other process.
While in the lab, I also made a series of tutorial videos for the equipment in the lab. I did all the writing, shooting, editing, scoring, and graphic design for the videos. I would love to share them, but they're technically confidential. They are the funniest heavy machinrey tutorials I have ever personally seen; how many other x-ray CT guides have an after-credits sequence?